Purging Compound for Short Cleaning Times and Minimal Downtime
With our “EASYClean 380C” purging compound, you can achieve fast color changes and easy operation for minimized machine downtimes with an application range of 170 to 380°C (338 to 716°F)!
Purging Challenges in the Plastics Industry
In injection molding and extrusion, companies face numerous challenges when purging the plasticizing units of injection molding and extrusion machines.
- High reject rates and low machine efficiency: Dirty machines often lead to production errors such as uneven surfaces, dimensional deviations or color errors. This results in increased rejects and reduces the productivity of your systems.
- Time-consuming color and material changes: Long changeover times between different materials or colors cause unnecessary production downtimes and increase costs.
- Difficult handling of common purging compounds: Many conventional purging agents are complicated to use, require special expertise and are often not suitable for all materials or temperature ranges.
- Insufficient purging results: Many purging compounds do not deliver the desired results that simplify your processes or enable a quick material or color change. Our purging compound, on the other hand, impresses with their efficiency - try them out and see for yourself!
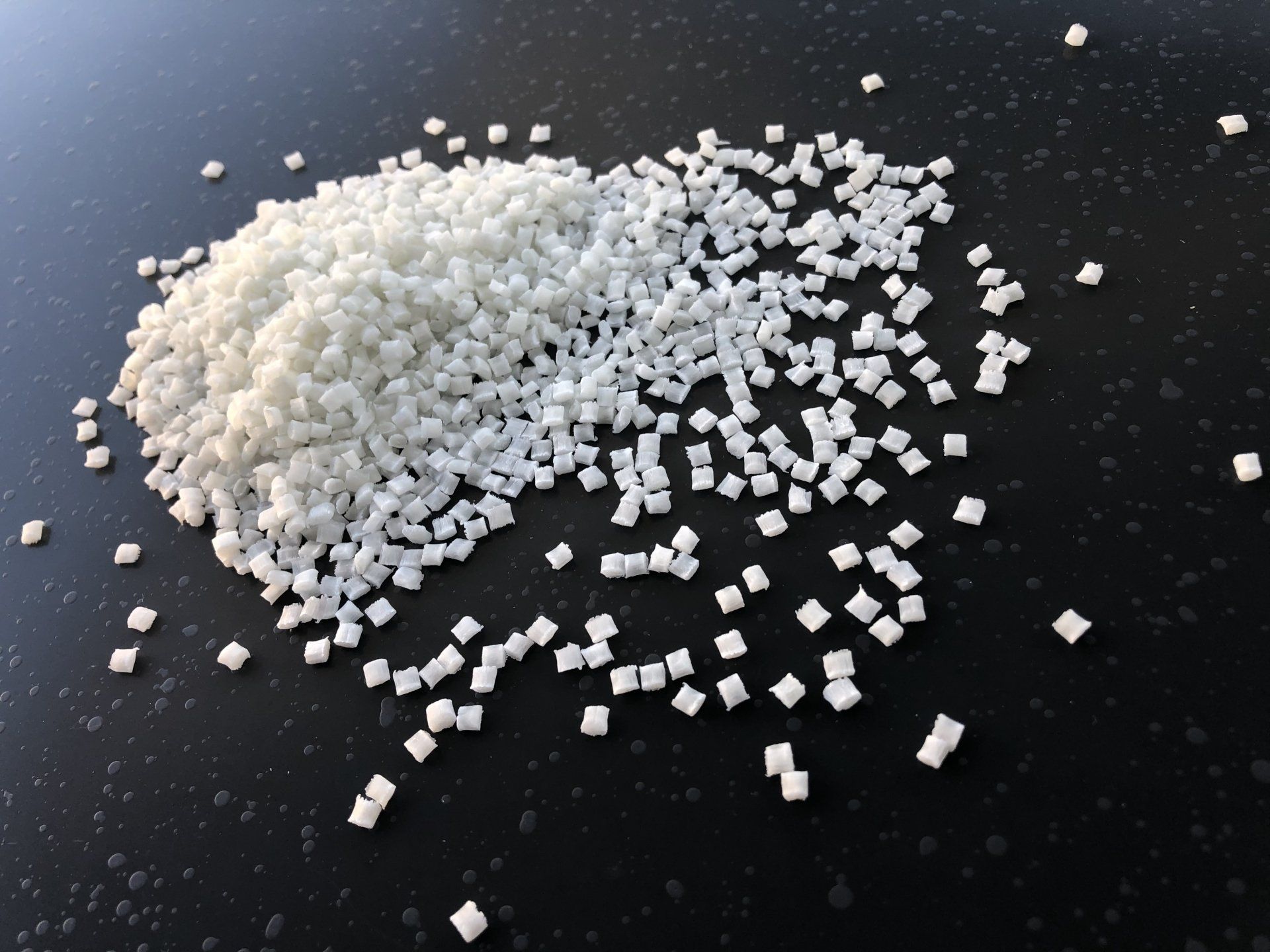
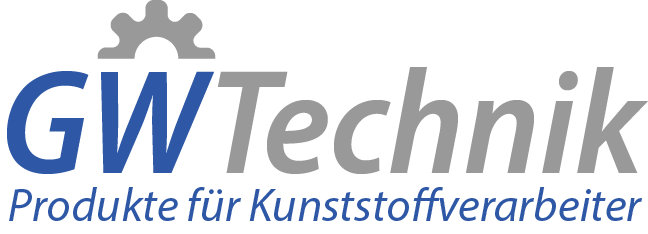
EasyClean 380C: Product Features and Benefits
Our EasyClean 380C removes all residues, impurities and ink residues from the screw, cylinder and hot runner. With our easy-to-understand application instructions, our purging compound is also very easy to use.
Easy to use and handle
Wide temperature range
Effective color change and crystal-clear material
Versatile Application
Low consumption
Little odor and suitable for hot runners
Areas of Application for Our Purging Compound
Injection Molding
In injection molding production, purging compounds are particularly valuable for removing impurities in the screws and cylinders of the machines. They help to remove material residues and buildup between production runs, enabling quick and efficient color or material changes. This reduces waste, shortens downtimes and optimizes the quality of the manufactured parts by avoiding defects such as color deviations or uneven surfaces.
Extrusion
In extrusion processes where plastic is processed continuously, material build-up and impurities can occur in the screws and nozzles. The use of purging compounds ensures that these residues are removed quickly and thoroughly, thereby maintaining process stability and product quality. Particularly in the case of color or material changes, which frequently occur in extrusion, purging compounds help to make the change smooth and efficient.
Hot Runner Systems
Thorough purging is crucial in hot runner systems, as even the smallest material residue can affect the quality of the end product. Purging compounds help to remove impurities in the channels and nozzles without damaging the sensitive components of the system. They prevent blockages and deposits that could lead to faults in the injection molding process, thus helping to extend the lifespan of the hot runner technology.
Screw cleaning
Efficient purging of screws is essential to remove material residues and buildup that can disrupt the production process. Purging compounds offer a quick and easy way to thoroughly clean screws during color or material changes. They minimize the risk of contamination and ensure consistently high production quality with minimal downtime.
Benefits of Our Purging Compound for Your Company
Wide Range of Application Areas
A good purging compound offers you numerous advantages. It ensures efficient and thorough purging of plasticizing units of injection molding machines, (screw) extruders and hot runners.
Fast Color and Material Changes
The quick removal of paint residues and impurities speeds up material and color changes, minimizing downtimes. A good purging compound is also suitable as a freezing mixture (“sealing”) for longer downtimes (e.g. weekends).
Less Waste and Environmentally Friendly
Another advantage is the reduction of rejects and production errors, as a clean screw ensures consistent and defect-free products. Ultimately, many purging compounds are formulated to be environmentally friendly, which not only reduces operating costs but also protects the environment.
Videos of our Purging Compound
Watch example videos of our purging compound from our customers here:
These and many other customers trust our products
Contact
Would you like to know more about our products or receive a quote? Then send us a non-binding inquiry now!